James Walsh Central Saint Martins’ Gepetto of Porcelain Dolls
- kwertz1120161
- May 26, 2020
- 4 min read
Updated: Jun 30, 2020
For his final graduate collection, Central Saint Martin’s Womenswear student, James Walsh, made the bold choice to charter unknown territory and explore the capabilities of 3D printing.
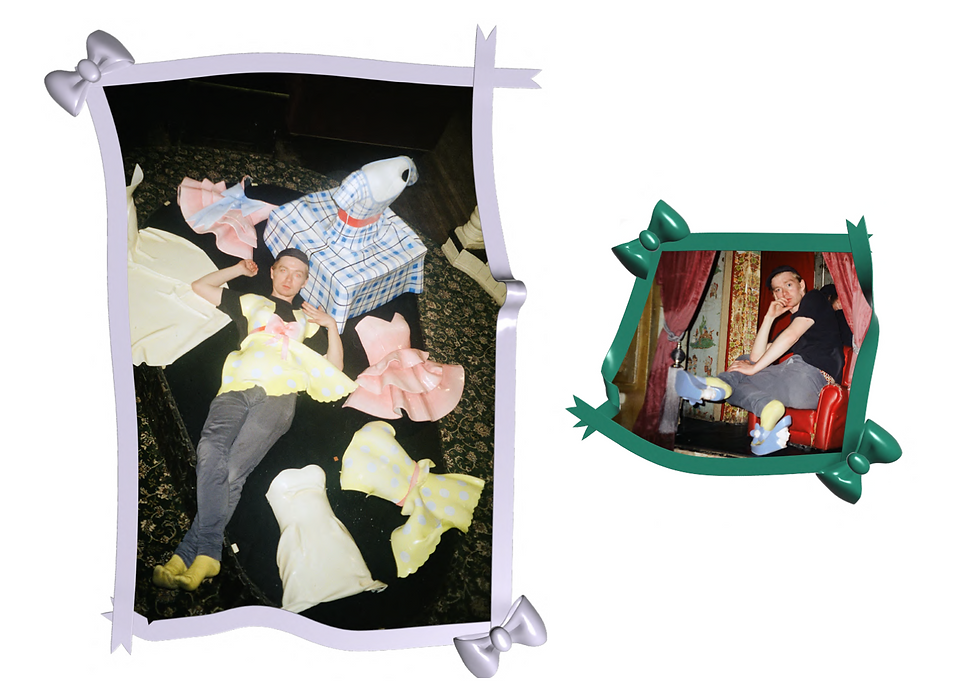
As 2020 continues to interrupt our daily lives, discussions regarding the fashion industry and how it will survive in a post COVID-19 world are at the forefront of every fashion discussion. Where will it go? How will we get there? Do we really have to re-evaluate the entire inner workings of the fashion industry? Well, it is important to look towards not only the innovators trying to change the world with fantastical dreams turned reality through technology but also to the soon-to-be graduates, or MA students that stumbled upon innovation by happenstance.
CSM womenswear designer, James Walsh, didn’t necessarily plan his final collection around the use of cutting edge technology, nor was he hell-bent on creating waves or trailblazing the use of technology within the fashion space; instead, he simply needed to find a means to an end. A way to make the theme of his collection come to still-life.
“Because my collection is based on static sculptures like statues and monuments or porcelain dolls and polly pockets, my only real options were to sculpt the designs myself or have them 3D printed. But I’m not a sculptor, I don't have those techniques, so I went with 3D printing instead,” Walsh said in an interview with S.I.R.I.U.S.

His relaxed tone and blasé demeanour surrounding the impressive innovation used throughout his garments rolled off his back as if he has been using these techniques for years, but he would have you fooled.
“Knowing the restrictions I had in my design concept for creating the garments, I was looking into different ways of combining sculpture and garments and that’s when I came across CLO which was the digital printing software I used,” the womenswear designer said.
CLO is a software allowing 2D fashion patterns to be digitally sewn together and draped without the traditional toiling process or material waste. James explained that the printing was easy as he could render the designs on screen and with the mere click of a button the garment would begin to print. He also pointed out, however, that,
“It was hard because the pieces were all printed in different bits as the printer couldn't print the whole garment, so trying to get them to fit together and match up provided some difficulty.”
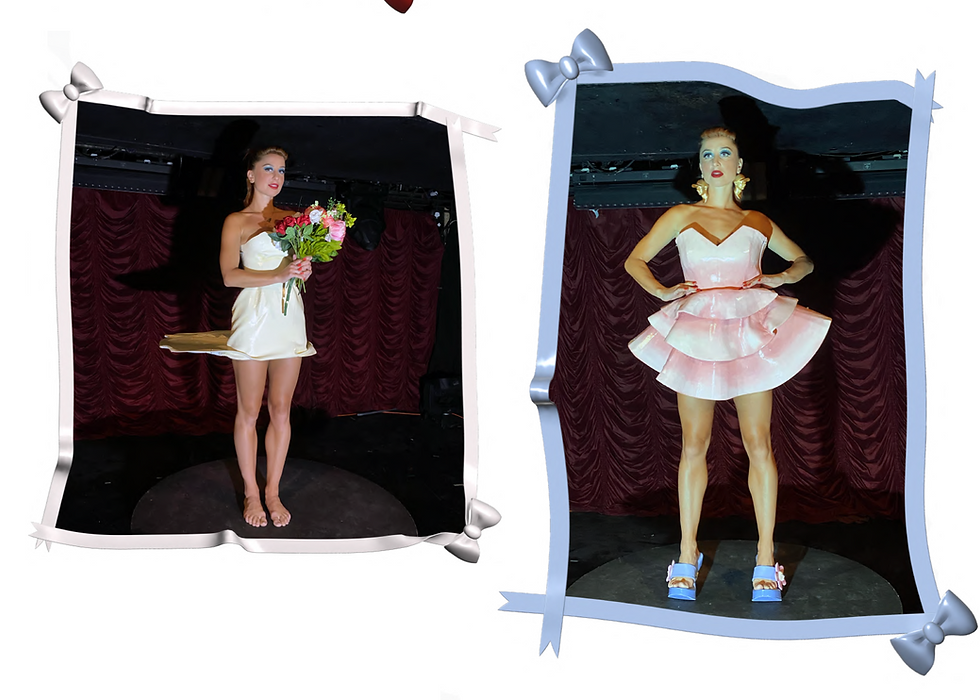
His inspiration derives from manmade objects, such as static clothing on statues, sculptures, plastic toys and porcelain dolls as he was enthralled by how the frozen nature of the garments lent a sense of timelessness of the figures. In order to replicate this theme of frozen structure throughout his collection, he needed to find a way to make the complex and technical processes more easily accessible, which he did. CLO’s way of bringing James’ 2D sketches to life
allowed him to experiment and find a link between extractiong elements from the CLO software, in order to create garments that could be held in a fixed position (like a porcelain doll or statue), scaled up and then printed out. He was able to play around with highly detailed and manipulated drapes with complete control of the final product throughout.
“I was also able to achieve things not possible by traditional sculpting processes, as all of my design development was digital. I honestly just needed a way to realise my designs. I didn’t even really know how sustainable it was until my teacher and I spoke about it. And now my whole collection is entirely zero-waste and the material I used to print is completely recycled and biodegradable as well,” Walsh explained.
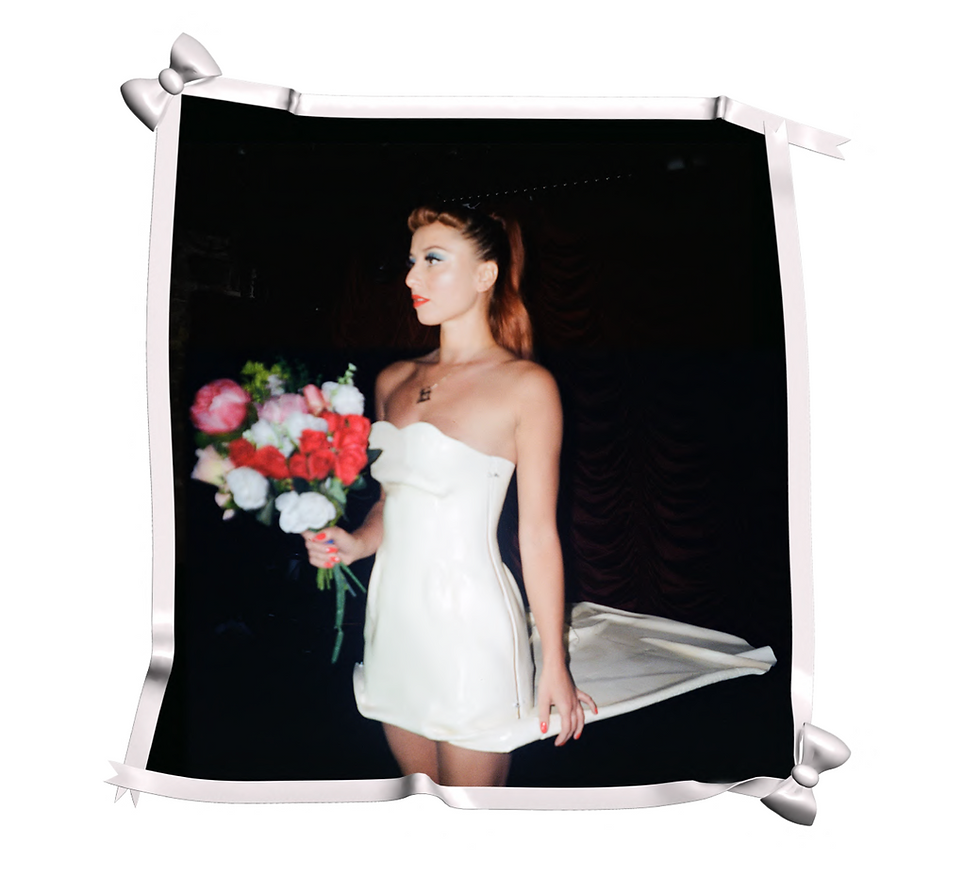
“By using something like CLO, as a young and creative designer I was granted the opportunity to not only make my wildest concepts of Sylvanian family-inspired, statuesque garments come true, but I was given the opportunity to also learn more about 3D printing and how it works because it was an accessible program.”
Unfortunately, during his BA, Walsh was forced to work quickly as the corporation that sponsored him with the printer as they needed it returned prior to the collection deadline, hindering him from being able to fully explore his capabilities.
After acknowledging the major benefits of 3D printing, such as its sustainability, efficiency, the use of biodegradable materials, and (most importantly), the ability to go to the pub while a machine prints your collection, James intends to continue to use 3D printing for his future collections. As he transitions from his BA womenswear course at CSM to an MA course next year, he hopes to continue to explore the endless possibilities granted to him through 3D printing, hoping to develop his design agenda, explore the varying ideas that revealed themselves throughout the process of this collection, and create movable 3D printed garments.

It is designers like James who are the future of our industry. Their ability to adopt new innovation so seamlessly with their collection and vision is admiring and gives insight into the mindset of the new generation of designers. A generation who believes that innovation is cool, sustainability is cool, and adopting a slightly more unorthodox approach to design is also cool. Technological advances are slowly becoming more commonplace, but nevertheless it is great to see Walsh adopt an entirely new technique and use experimentation in order to achieve his design goals.
Comments